Production Standards
BENEFITS
Tough. Durable. Versatile.
Vitreous enamel will not rust, is resistant to chemical attack, abrasion and fire as well as being more durable than any other architectural cladding coating.
Its versatility enables custom designs of all shapes and dimensions, the use of graphics and logos as well as a virtually unlimited colour range. 
Non Static
Does not collect dust or allergens.
Fire Resistance
Vitreous enameled panels have an ignitability index of 0, spread of flame index of 0, heat evolved index of 0 and smoke developed index of 1 according to AS NZ 1530.3 and are non combustible to BS 476 Part 4, have a fire propagation index of 0 to BS 476 Part 6 and have a Class 1 spread of flame classification to BS 476 Part 7.
They are an ideal replacement for combustible cladding and have a superior fire performance to all main architectural cladding materials.
Graffiti Resistant
Non stick, non porous, chemical resistant, extremely hard and color fast. Any painted or written graffiti on the coating can be entirely removed without affecting the performance of the panel. No stains. No discolouration.
Thermal Shock Resistance
Vitreous enameled coated steel will withstand rapid cooling by water spray from +400┬░C to normal room temperatures over a 30 second period.
Safety
The resistance of vitreous enameled steel to impact and distortion under extreme conditions provide further significant safety advantages in applications such as tunnels and claddings in public areas. 
Non Porous
Like glass, vitreous enamel is completely non porous which prevents harmful bacteria or residual chemicals from being absorbed into the enamel surface. When an enamel surface is cleaned with anti-bacterial solutions it is truly sterile and germ free.
Printable Coating
Vitreous enamel panels can be silkscreened or direct printed with high resolution multi-coloured graphics.
Images or graphics will be a vitreous enamel coating with the same durability and performance characteristics.
Electrical Safety
Vitreous enamel panels can assist with insulating against electrical currents or, if the enamel is penetrated, can be used as an earth point.
Dielectric strength of ordinary vitreous enamels will range from 200 to 500 volts per mil with an average of 4 to 6 mm total thickness.
Environmental Safety
The production of VE panels is an environmentally friendly process that does not involve harmful substances.
The panels are made from non toxic materials including glass and steel.
Materials are not harmful to the environment and are recyclable. The VE coating increases the lifespan of the original steel many times thereby reducing waste and the number of times the steel needs to be reprocessed.  VE Panels release no toxic fumes.
Non stick, easy to clean
High lubricity, non stick and non porous make it very easy to clean with a mild detergent solution or anti-septic chemical cleaners.
High Impact Resistance
The physical strength of the steel, coating and panel backing enable vitreous enameled panels to withstand deformation and damage due to impact. Panels are quick to install and easily replaced.
Lower Maintenance Costs
Non Stick and non static vitreous enamel attracts less dirt and harmful bacteria. Extremely high abrasive resistance ensures no scratching during regular cleaning cycles and therefore no loss in anti-bacterial quality of the smooth vitreous enamel coating. Panels can easily be kept sterile with no loss in quality over time.
High Chemical Resistance
Vitreous enamels are formulated with relatively inert inorganic oxides. This provides an impervious surface that is highly resistant to chemicals that may be used in medical, manufacturing or convenience clean room environments. This includes: Strong Acids at any temperature up to 191⁰C (with the only exception of hydrofluoric acid). Alkalis : Up to maximum pH of 12 at 100⁰C. Also including organic acids and solvents, oils and soil corrosion.
High Resistance to Abrasion
A combination of very high lubricity and extreme surface hardness gives vitreous enamel unusually high abrasive resistance when compared to other cladding surfaces. On the Moh Hardness Scale : Diamond =10, Aluminium or Sheet Steel=3 Resin Coatings = 2.5 – 3 Vitreous Enamel = 5 to 6. This high abrasive resistance ensures no scratching during regular cleaning cycles and no loss in anti bacterial quality of the smooth vitreous enamel coating.
Our products are manufactured to internationally recognised standards which ensures consistent product quality supported by warranties of up to 50 years depending application.
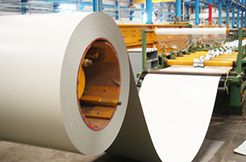
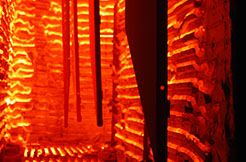
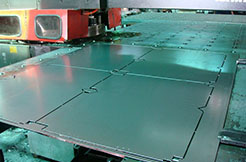
Production of our VE panels complies with the following international product and management standards:
MANUFACTURING STANDARDS | ||||
BS EN ISO 28722 | Vitreous and porcelain enamels ΓÇô Characteristics of the enamel coatings applied to steel panels intended for architecture | |||
CNS 12809 (China National Standard) | Porcelain enamelled steel panels | |||
JIS A 6516 (Japan International Standard) | Porcelain enamelled steel panels | |||
BS 3830: 1973 | Specification for Vitreous Enamelled Steel Building Components | |||
ISO 9001 | Quality Management Systems | |||
ISO 14001 | Environmental Management Systems | |||
ISO 18001 | Occupational Health and Safety Management Systems |
BENEFITS
Tough. Durable. Versatile.
Vitreous enamel will not rust, is resistant to chemical attack, abrasion and fire as well as being more durable than any other architectural cladding coating.
Its versatility enables custom designs of all shapes and dimensions, the use of graphics and logos as well as a virtually unlimited colour range. 
Non Static
Does not collect dust or allergens.
Fire Resistance
Vitreous enameled panels have an ignitability index of 0, spread of flame index of 0, heat evolved index of 0 and smoke developed index of 1 according to AS NZ 1530.3 and are non combustible to BS 476 Part 4, have a fire propagation index of 0 to BS 476 Part 6 and have a Class 1 spread of flame classification to BS 476 Part 7.
They are an ideal replacement for combustible cladding and have a superior fire performance to all main architectural cladding materials.
Graffiti Resistant
Non stick, non porous, chemical resistant, extremely hard and color fast. Any painted or written graffiti on the coating can be entirely removed without affecting the performance of the panel. No stains. No discolouration.
Thermal Shock Resistance
Vitreous enameled coated steel will withstand rapid cooling by water spray from +400┬░C to normal room temperatures over a 30 second period.
Safety
The resistance of vitreous enameled steel to impact and distortion under extreme conditions provide further significant safety advantages in applications such as tunnels and claddings in public areas. 
Non Porous
Like glass, vitreous enamel is completely non porous which prevents harmful bacteria or residual chemicals from being absorbed into the enamel surface. When an enamel surface is cleaned with anti-bacterial solutions it is truly sterile and germ free.
Printable Coating
Vitreous enamel panels can be silkscreened or direct printed with high resolution multi-coloured graphics.
Images or graphics will be a vitreous enamel coating with the same durability and performance characteristics.
Electrical Safety
Vitreous enamel panels can assist with insulating against electrical currents or, if the enamel is penetrated, can be used as an earth point.
Dielectric strength of ordinary vitreous enamels will range from 200 to 500 volts per mil with an average of 4 to 6 mm total thickness.
Environmental Safety
The production of VE panels is an environmentally friendly process that does not involve harmful substances.
The panels are made from non toxic materials including glass and steel.
Materials are not harmful to the environment and are recyclable. The VE coating increases the lifespan of the original steel many times thereby reducing waste and the number of times the steel needs to be reprocessed.  VE Panels release no toxic fumes.
Non stick, easy to clean
High lubricity, non stick and non porous make it very easy to clean with a mild detergent solution or anti-septic chemical cleaners.
High Impact Resistance
The physical strength of the steel, coating and panel backing enable vitreous enameled panels to withstand deformation and damage due to impact. Panels are quick to install and easily replaced.
Lower Maintenance Costs
Non Stick and non static vitreous enamel attracts less dirt and harmful bacteria. Extremely high abrasive resistance ensures no scratching during regular cleaning cycles and therefore no loss in anti-bacterial quality of the smooth vitreous enamel coating. Panels can easily be kept sterile with no loss in quality over time.
High Chemical Resistance
Vitreous enamels are formulated with relatively inert inorganic oxides. This provides an impervious surface that is highly resistant to chemicals that may be used in medical, manufacturing or convenience clean room environments. This includes: Strong Acids at any temperature up to 191⁰C (with the only exception of hydrofluoric acid). Alkalis : Up to maximum pH of 12 at 100⁰C. Also including organic acids and solvents, oils and soil corrosion.
High Resistance to Abrasion
A combination of very high lubricity and extreme surface hardness gives vitreous enamel unusually high abrasive resistance when compared to other cladding surfaces. On the Moh Hardness Scale : Diamond =10, Aluminium or Sheet Steel=3 Resin Coatings = 2.5 - 3 Vitreous Enamel = 5 to 6. This high abrasive resistance ensures no scratching during regular cleaning cycles and no loss in anti bacterial quality of the smooth vitreous enamel coating.